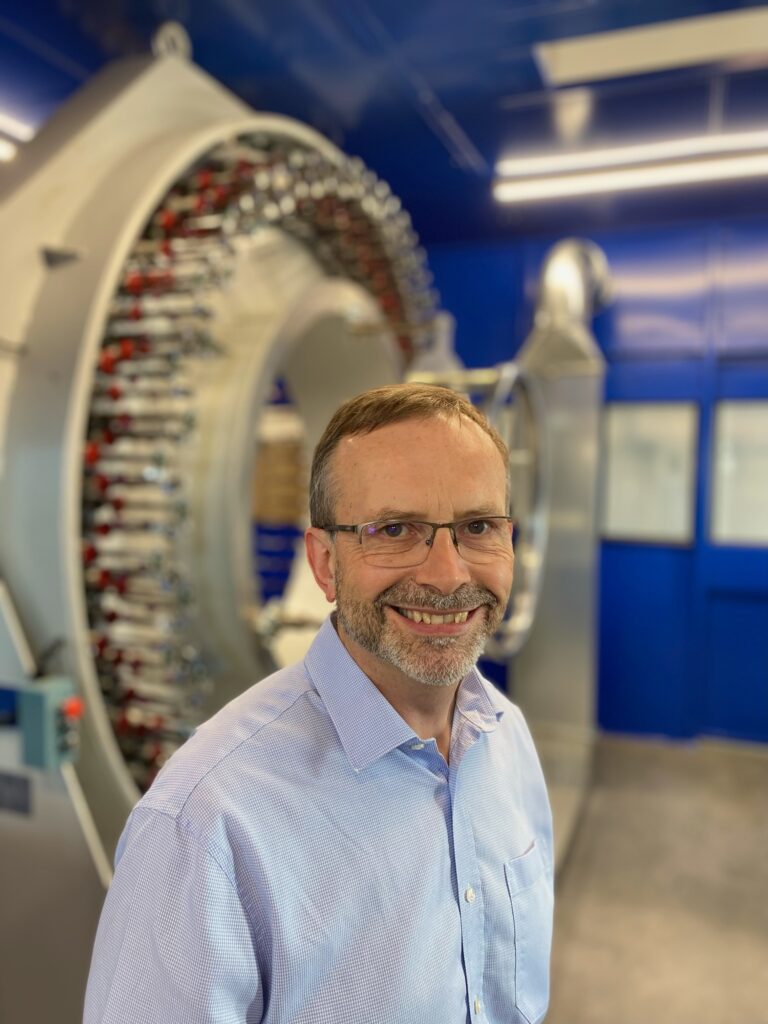
Composite Braiding is revolutionising composite manufacturing with its unique braiding process, offering a faster, more sustainable, and cost-effective solution for the rail industry.
Managing Director Steve Barbour explains how the company’s innovation is shaping the future of rail infrastructure.
Composite Braiding challenges traditional methods with its highly efficient braiding process, which is capable of producing up to a mile of material per shift.
“Our goal is to provide high-performance components at lower costs while significantly improving sustainability,” said Steve.
At the core of this process is “commingled fibre”, a combination of reinforcement fibres such as carbon or glass and thermoplastics like nylon or polypropylene. This integration streamlines production, minimises waste, and enhances efficiency. Using patented heating and moulding techniques, preforms are converted into structural components within 5 to 10 minutes, an astonishing 97% reduction in production time compared to conventional methods. Additionally, energy consumption is cut by up to 99%, making this approach highly sustainable.
Real-world benefits for rail contractors
As part of the Clean Futures Accelerator, a programme dedicated to supporting clean technologies in the West Midlands transport sector, Composite Braiding has developed a lightweight, sustainable alternative to traditional steel for overhead line equipment (OLE).
With funding provided through the programme and testing carried out at the Black Country Innovative Manufacturing Organisation (BCIMO), the project includes an 8-metre vertical column and a 4-metre horizontal arm, designed to offer the same functionality as steel but with significant advantages:
- Reduced weight: These components are up to 85% lighter, requiring smaller foundations and reducing concrete use, which lowers costs and carbon emissions.
- Easier installation: Their lightweight nature simplifies transport and logistics, allowing contractors to use smaller installation equipment and reducing the need for costly access roads and heavy machinery.
- Sustainability: The materials are recyclable, aligning with the rail industry’s circular economy principles and reducing emissions during transport and installation.
- High-volume, low-cost production: Automation ensures scalability and affordability while maintaining consistent quality.
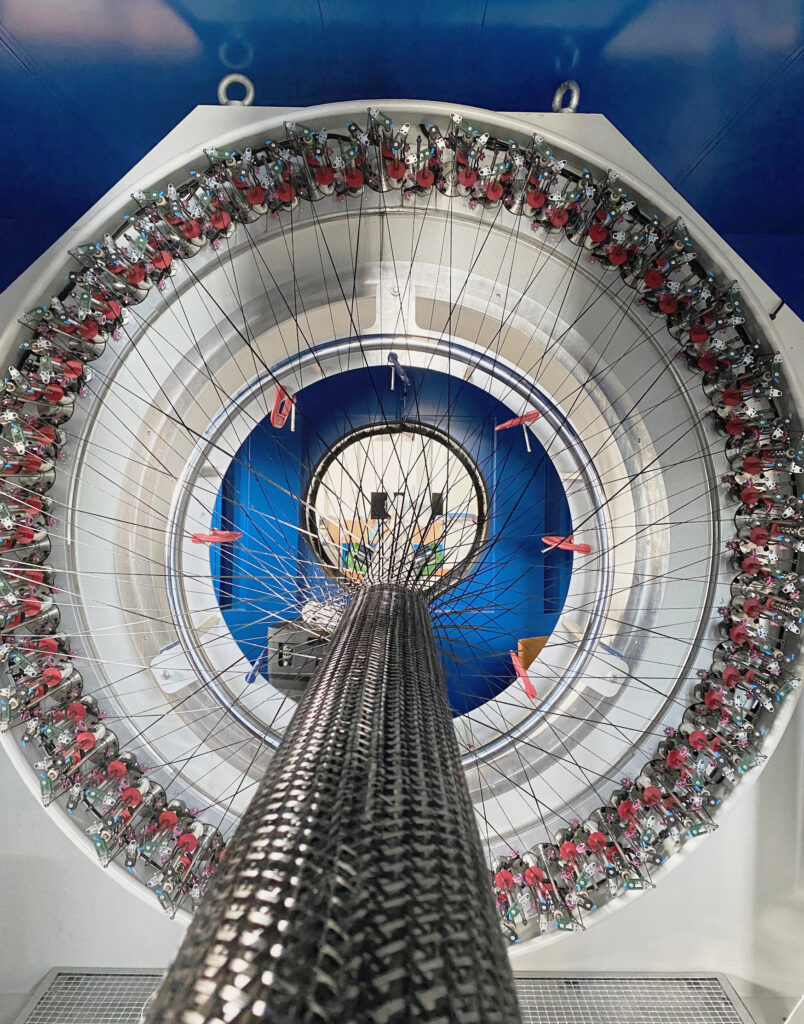
Overcoming adoption barriers
The rail industry has long relied on traditional materials, making the adoption of new technologies a challenge. “We understand the hesitation that comes with innovation,” said Steve. “That’s why we’re actively working with rail organisations to validate our technology.”
Through the Clean Futures Accelerator Programme, Composite Braiding has access to BCIMO’s Rail Development & Test Site, where its OLE components are being rigorously tested against industry standards. “By the time contractors reach GRIP 3 (option selection) under Network Rail’s PACE framework, they will have the data and confidence to consider our solution as a viable, low-risk alternative,” Steve added.
Future applications beyond rail
While the current focus is on rail infrastructure, Composite Braiding’s technology has broad applications, from 5G masts to highway structures. “Our process allows us to create complex shapes with minimal waste, opening up opportunities in telecoms, highways, and beyond,” says Barbour.
The Clean Futures Accelerator and BCIMO’s Demo Day
The Clean Futures Accelerator programme has played a crucial role in fast-tracking the development of Composite Braiding’s innovations. With funding, technical expertise, and commercial support, the company has been able to advance its technology at an accelerated pace.
In February 2025, Composite Braiding showcased its new, ultra-lightweight twin-track cantilever OLE solution to delegates from across the rail industry at BCIMO’s exclusive Demo Day.
The structure on display weighed just 277kg (84% lighter than those currently on the market), with its manufacture and transport producing 70% less CO2e emissions than typical steel structures.
Commenting on the day, Steve said: “This event was a brilliant opportunity to demonstrate how our technology meets the industry’s sustainability and efficiency goals,”
“It gave us a chance to engage with industry leaders and show the real-world impact of our innovation.” He added.
Transforming industries
Composite Braiding’s technology is not just about better materials, it’s about transforming industries. By combining lightweight design, scalable production, cost-effectiveness, and sustainability, the company provides a compelling alternative to traditional manufacturing methods.
“We’re excited to be leading this change and working with partners who share our vision for a cleaner, smarter future,” said Steve. “We invite industry professionals to speak to us firsthand to find out how our innovation is shaping the future of rail and beyond.”
For more information, visit: https://compositebraiding.com