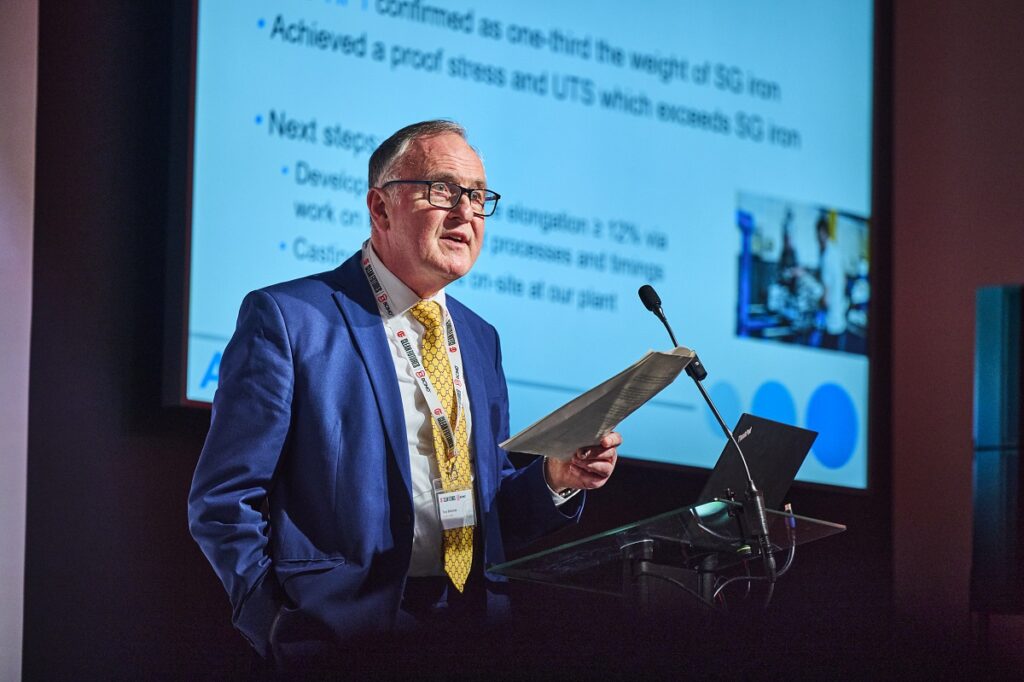
AluCast is a West Midlands-based foundry which has operated for more than 50 years. In this article, Tony Sartorius, AluCast’s Chairman, explains how the business’s innovative high-strength aluminium alloy can provide a unique low carbon alternative to traditional materials used in rail manufacturing.
At AluCast, we have always been driven by innovation, precision, and a commitment to solving real-world challenges. Over 57 years, we’ve built a reputation for producing high-quality aluminium components, serving industries such as automotive, rail, industrial and other manufacturing sectors. Today, with 108 dedicated employees and a £10 million turnover, we are proud to carry that expertise into developing alternative solutions to help decarbonise the transport industries for a cleaner future.
The Clean Futures Accelerator program, which we were awarded a place on in 2024, provided us with a unique opportunity to showcase our unique material innovation—a high-strength, lightweight aluminium alloy capable of rivalling the properties of SG iron while aligning with the rail industry’s net zero goals. Supported by BCIMO’s Rail Development and Test Site, we have explored our technical capabilities to deliver stronger, more sustainable solutions for the transportation of tomorrow.
Lighter, greener rail components
The rail industry is under pressure to decarbonise while improving performance, safety, and efficiency. At AluCast, we believe aluminium has a critical role to play in this transition. Our innovation focuses on developing a high-strength aluminium alloy that is two-thirds lighter than SG iron, offering significant energy savings and carbon reduction opportunities.
What sets this material apart is its ability to achieve similar tensile strength and ductility to SG iron through precise casting and advanced heat treatment processes. With over 50 years of expertise in sand, gravity, high-pressure, and low-pressure casting, we are perfecting the technical capabilities required to meet the mechanical demands of structural rail components while also cutting down weight and emissions.
By reducing the mass of rail vehicles, our solution can help operators achieve greater energy efficiency. Every kilogram saved translates into lower fuel consumption or reduced energy demands, which are key steps in achieving the industry’s net zero targets.
Developing high-strength aluminium solutions
Our innovation journey began with making sand cast prototypes, as well as production parts for military applications and traditional parts for civilian use. We are now progressing to both gravity and low-pressure casting methods. This approach offers better control over the material’s properties, enabling us to optimise strength and durability while ensuring cost efficiency. The objective of the research is to develop an aluminium alloy that can potentially achieve strength comparable to SG Iron 420:12, a benchmark material for components in the rail industry.
To validate these claims, we have conducted rigorous testing and demonstrated our results at BCIMO’s Rail Development and Test Site. Using tensile testing machines, we have compared our new high-strength alloy against traditional materials, such as A356 aluminium. Visitors to our demonstration day at BCIMO in February saw the full testing process in pulling test bars and video footage showing casting being heat treated, machined, and tensile tested.
Our technical demonstration included:
Machining: Test bars were machined to precise dimensions on a lathe to prepare them for tensile testing.
Tensile Testing: Pulling test bars measured yield strength, ultimate tensile stress, and elongation. Data was displayed in real time, highlighting the superior performance of our alloy.
Delivering performance without the emissions
At AluCast our work aligns closely with the rail industry’s environmental goals. The lightweight nature of our high-strength aluminium offers significant benefits, including:
- Reduced carbon emissions: Lower vehicle weight translates into decreased energy consumption, whether trains run on diesel or electricity
- Energy-efficient manufacturing: Our processes require significantly less energy compared to traditional iron or steel production, further reducing the carbon footprint
- Circular economy benefits: Aluminium is infinitely recyclable, making it an ideal material for a sustainable rail supply chain
As the industry continues to invest in new vehicles and refurbishment programs, AluCast’s lightweight solutions are well-suited to support both original equipment manufacturers (OEMs) and rail refurbishment initiatives. Whether used in structural components, interiors, or other applications, our materials deliver performance without the carbon outputs of traditionally used solutions.
Decades of expertise and experience
While molten metals and eye-catching casting processes capture the imagination, the true value lies in the technical expertise behind our components. At AluCast, we pride ourselves on combining traditional craftsmanship with R&D and technical innovation. From our engineering managers’ decades of hands-on experience to advanced simulation tools used by our technical team, we bring a deep understanding of materials, physics, and manufacturing processes.
This expertise enables us to go beyond the expected, producing components that meet stringent tolerances and exceed performance expectations.
Demonstrating the future of rail
The Clean Futures Accelerator has given us a platform to demonstrate how aluminium can drive the rail industry forward, achieving the perfect balance of strength, weight, and sustainability. As we continue to refine our processes and test our materials, we remain committed to contributing to a cleaner, greener future for rail.
Following our presentation at the Clean Futures Accelerator demonstration day at BCIMO, we are now looking to showcase not only the strength of our materials but also the strength of our team and our commitment to innovation. We look forward to bringing our aluminium solutions to the industry and collaborating with stakeholders to turn these possibilities into reality.
For more information visit https://www.alucast.co.uk/